Turning a 3-axis cnc machine into a 5-axis cnc machine
CNC machines have revolutionized manufacturing by offering precision, efficiency, and automation in creating complex parts. While 3-axis CNC machines are common and capable of handling a wide range of tasks, some projects require the advanced capabilities of a 5-axis machine.
Upgrading from a 3-axis to a 5-axis CNC machine can significantly enhance your ability to produce precise components. This article will guide you through the process of converting a 3-axis CNC machine into a 5-axis machine. We’ll cover the necessary steps, components, and considerations to ensure a successful upgrade, allowing you to expand your machining capabilities and improve production outcomes.
What Is a CNC Machine?
A CNC machine is a type of machine tool operated by computer software to perform various tasks with high precision. These machines are used in manufacturing to automate the control of tools like lathes, mills, drills, and routers. The key feature of CNC machines is their ability to follow detailed instructions provided by a computer program, allowing for accurate and repeatable production.
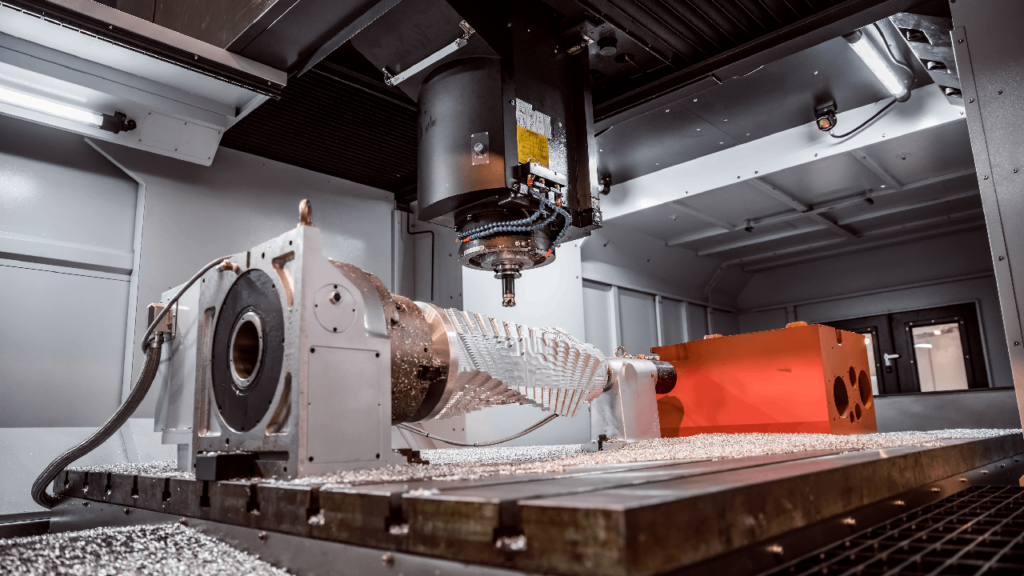
A cnc machine at work
They work by interpreting a computer-generated design file. This file contains a set of instructions, called G-code, which tells the machine how to move its tools to shape, cut, or drill the material. The process starts with a digital design created using CAD (Computer-Aided Design) software. This design is then converted into a G-code that the CNC machine can understand and execute.
CNC machines come in various types, each suited to different tasks. For example, CNC milling machines use rotating cutting tools to remove material, creating precise shapes and surfaces. CNC lathes, on the other hand, rotate the material itself while a cutting tool shapes it, making them ideal for creating cylindrical parts. CNC routers are often used for cutting and engraving wood, plastics, and other softer materials.
In addition to their precision, CNC machines are also known for their efficiency. Once programmed, they can operate continuously with minimal human intervention, increasing productivity and reducing labor costs. This automation also helps to minimize errors and ensure consistency in the production process.
Is CNC Equal to CNC Machining?
CNC, or Computer Numerical Control, is a technology that automates the control of machine tools through a computer. It uses pre-programmed sequences to control machinery precisely and efficiently. This technology is applied to a wide variety of machines, including lathes, mills, routers, and grinders. Essentially, CNC is the brain that controls the machinery, telling it what to do and how to move to perform specific tasks.
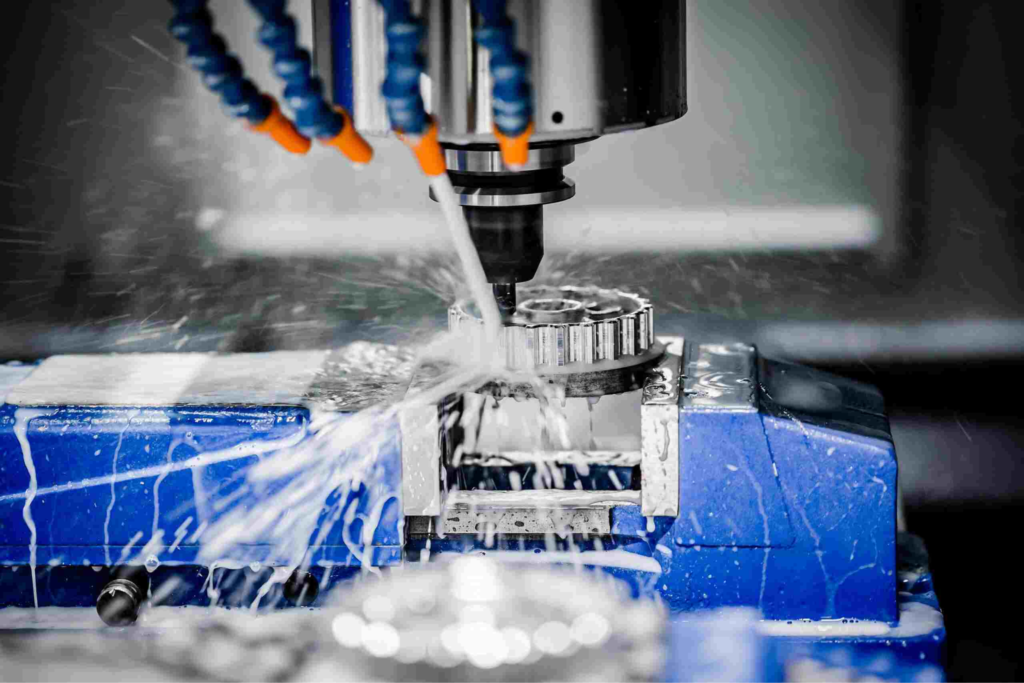
Typical cnc machining process
CNC machining, on the other hand, refers to the actual process of manufacturing parts using machines controlled by CNC technology. This process involves various operations such as drilling, milling, turning, and more. During CNC machining, raw material is cut, drilled, or shaped to create a finished product. The CNC system ensures that these operations are carried out with high precision and accuracy, which is essential for producing complex and detailed parts.
While CNC and CNC machining are closely related, they are not the same thing. CNC is the system and technology that controls the machinery. It is the software and the control mechanism that makes precise automation possible. CNC machining is the practical application of this technology to produce parts and components. It involves the actual cutting, shaping, and finishing of materials to create a specific product.
CNC machining encompasses several techniques including milling, turning, 5-axis machining, and drilling.
- Milling uses CNC mills to remove material from a stationary workpiece using tools like lathes and water jets. These mills can move along multiple axes (X, Y, Z, and sometimes A and B), enabling precise horizontal, vertical, and angled milling. This versatility reduces the need for repositioning the material, increasing efficiency in manufacturing intricate parts from wood, metal, and plastic.
- Turning involves rotating the workpiece at high speeds while a stationary cutting tool shapes it. Unlike milling, the stock is attached to a turning mechanism, making it ideal for producing cylindrical parts.
- 5-axis CNC machining involves a tool moving in five directions around the workpiece. This allows for complex shapes to be machined in a single setup without manual repositioning, saving time and ensuring precision. Movements include the standard X, Y, Z axes plus two additional rotary axes (A and B), enabling operators to approach the material from any angle.
- Drilling uses rotating tools to create precise round holes for screws and bolts.
- Grinding employs abrasive wheels to achieve high-precision surface finishes, far surpassing the accuracy of additive manufacturing.
- Cutting techniques like sinker and wire EDM use electrical discharge to cut materials without direct contact, providing precision cutting for complex shapes.
- Laser cutting, often part of sheet metal fabrication, is also integrated into CNC processes, highlighting the versatility and precision of CNC technology in various applications.
3-axis Vs 5-axis CNC Machines
Understanding the differences between 3-axis and 5-axis CNC machines helps in choosing the right one for specific manufacturing needs.
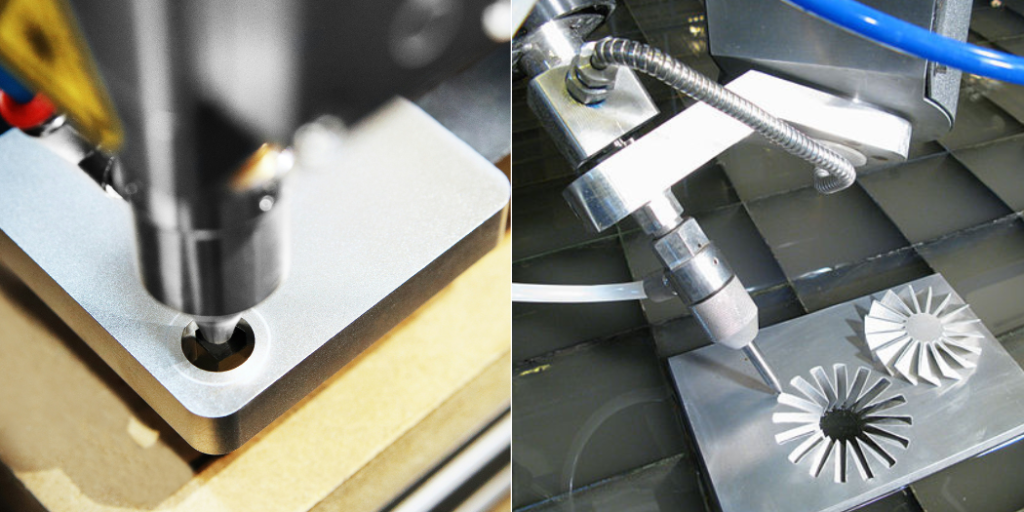
3-axis vs 5-axis CNC machines
A 3-axis CNC machine operates along three primary axes: X, Y, and Z. The X-axis moves left and right, the Y-axis moves forward and backward, and the Z-axis moves up and down. This type of machine is ideal for simpler tasks where the material only needs to be worked on from one direction at a time. Common applications include drilling, milling, and basic contouring. 3-axis machines are widely used because they are easier to program and operate. They are also more affordable, making them a popular choice for small to medium-sized workshops.
On the other hand, a 5-axis CNC machine offers much greater flexibility and capability. In addition to the three primary axes, it includes two additional rotary axes. These extra axes allow the machine to approach the material from virtually any direction. This is particularly useful for creating complex shapes and intricate details that would be difficult or impossible to achieve with a 3-axis machine. For example, in the aerospace and automotive industries, 5-axis machines are used to manufacture intricate parts with high precision.
The primary advantage of 5-axis CNC machines is their ability to work on multiple sides of a part without the need for manual repositioning. This not only saves time but also improves accuracy and consistency. However, 5-axis machines are more complex and expensive. They require more advanced programming skills and are typically used in industries where the higher cost is justified by the complexity and precision of the parts being produced.
How to Turn a 3-axis to a 5-axis CNC Machine
Converting a 3-axis CNC machine to a 5-axis CNC machine involves significant modifications and considerations.
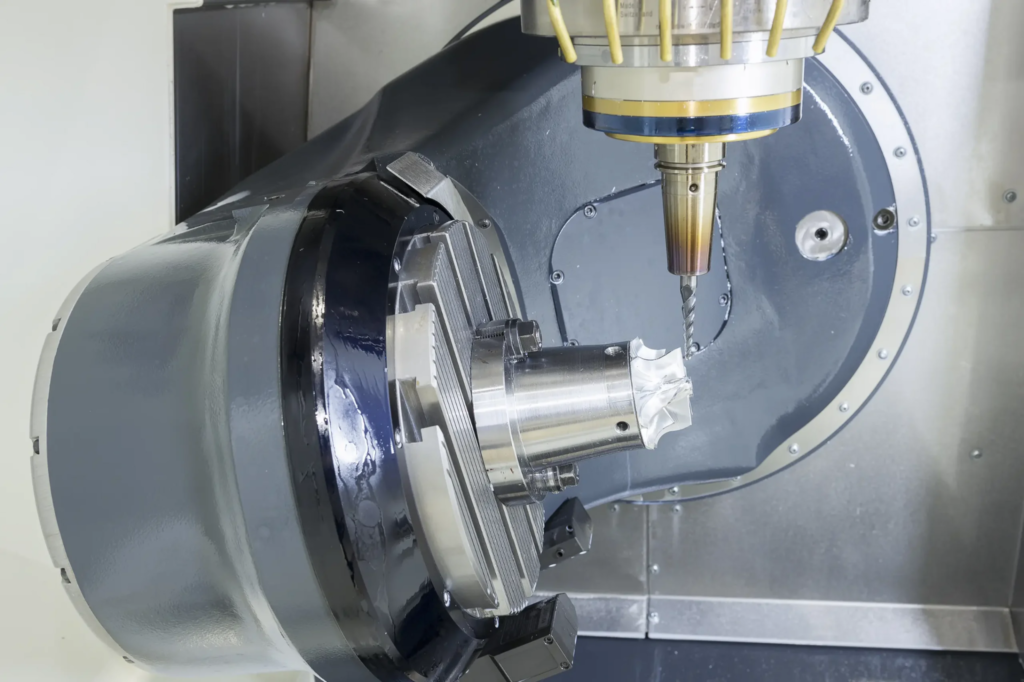
5-axis cnc machining process
Here are the main steps and factors involved in this process:
- Addition of Rotary Axes: The primary difference between a 3-axis and a 5-axis machine is the addition of two rotational axes (typically referred to as A and B axes). This can be achieved by integrating a trunnion table or a rotary swivel head into the existing 3-axis machine. The trunnion table offers the ability to rotate the workpiece, while the swivel head allows for the tool to be tilted.
- Mechanical Modifications: Installing rotary axes often requires mechanical modifications to the CNC machine. This includes adding the rotary components and ensuring they are precisely aligned with the existing axes to maintain accuracy. Upgrading the machine’s structural rigidity might also be necessary to handle the added complexity and movement of 5-axis operations.
- Control System Upgrade: The machine’s control system must be upgraded to handle the additional axes. This involves updating or replacing the CNC controller to support 5-axis simultaneous movements. Modern CNC controllers capable of 5-axis machining can generate more complex G-code that includes the rotational movements required for 5-axis machining.
- Software and Programming: Transitioning to 5-axis CNC machining requires new software that can handle the more complex programming. CAD/CAM software must be capable of generating toolpaths for 5-axis machining, taking into account the additional degrees of freedom. This software needs to be integrated with the machine’s controller.
- Calibration and Testing: After installing the new hardware and software, the machine must be carefully calibrated. This involves ensuring that all axes, both linear and rotational, are accurately aligned and synchronized. Extensive testing and adjustment are required to achieve the precision needed for 5-axis machining.
- Training and Expertise: Operating a 5-axis CNC machine is more complex than a 3-axis machine. Additional training for machine operators and programmers is essential to take full advantage of the capabilities of the new system and to ensure safe and efficient operation.
Conclusion
Transforming a 3-axis CNC machine into a 5-axis machine is a challenging but rewarding process. This upgrade involves adding two rotational axes, which enables the machine to handle more intricate and complex workpieces with greater accuracy and efficiency. While the conversion process requires careful planning, investment in additional components, and a solid understanding of CNC technology, the benefits are substantial.
Enhanced precision, the ability to create more complex geometries, and increased versatility can significantly boost your machining operations. By following the steps outlined in this article and taking into account the key considerations, you can successfully upgrade your CNC machine and unlock new potential in your manufacturing processes. This investment in technology can lead to higher quality products, greater customer satisfaction, and a competitive edge in the market.