CNC milling is a versatile machining process that uses computer-controlled rotary cutters to remove material from a workpiece. It is renowned for its ability to produce complex shapes and components with high precision and repeatability.
Maximizing efficiency involves streamlining setups, minimizing material waste, and leveraging advanced machining strategies to enhance productivity and competitiveness in manufacturing. You must explore the advanced capabilities to enhance your manufacturing operations today at https://www.xmake.com. Let’s check out more details about this!
Understanding CNC Milling Costs
Several factors affect CNC milling costs, including material type, design complexity, required tolerances, batch size, and machining time. Each of these factors can significantly impact the overall cost of a machining project.
Key cost components in CNC milling projects include raw material expenses, costs associated with tooling and fixtures, labor costs, depreciation of machining equipment, and overhead costs related to setup and ongoing operation.
Material Costs
The choice of material significantly influences CNC milling costs. Common materials like aluminum and steel vary in cost and machining characteristics, impacting overall project expenses based on their availability, hardness, and machining complexity.
Optimizing material selection involves balancing performance requirements with cost considerations. Strategies include choosing materials based on functional needs, considering alternatives with similar properties but lower costs, and evaluating the long-term benefits of durability and machinability.
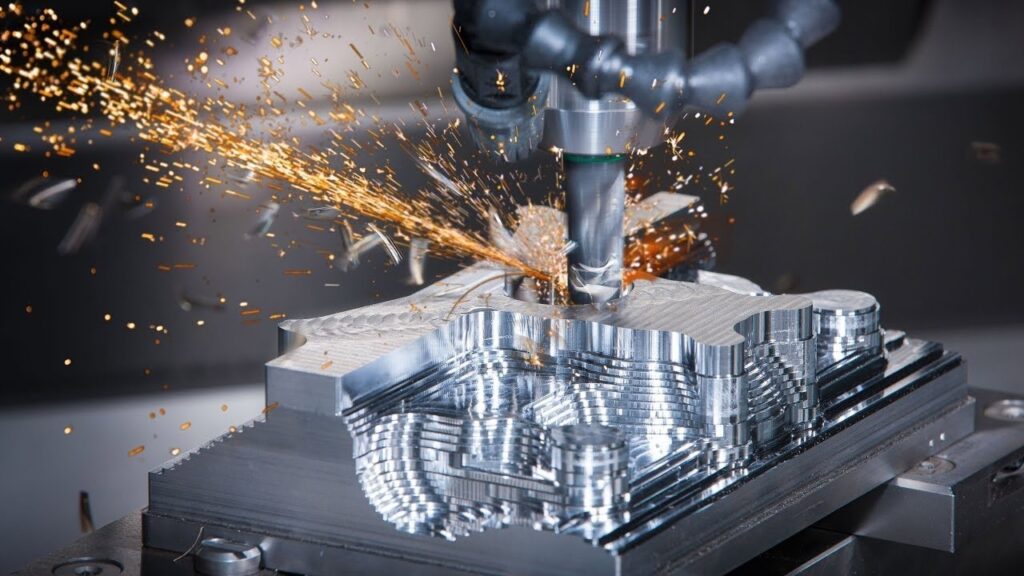
Tooling and Equipment Costs
Tooling is crucial in CNC milling for shaping and cutting materials with precision. High-quality tools ensure accuracy and efficiency, but their cost and maintenance impact overall project expenses significantly.
CNC milling equipment costs include initial purchase or lease expenses, maintenance, and depreciation over time. Understanding equipment depreciation helps in budgeting for replacements and optimizing the lifespan of machinery for cost-effective operations.
Setup and Programming Costs
CNC machine setup involves preparing tools, fixtures, and the workpiece for machining. Setup time directly influences production efficiency and costs, requiring skilled labor and efficient processes to minimize downtime.
Programming costs include the time and expertise required to create CNC machining programs tailored to specific parts and operations.
Operational Costs
Operational costs in CNC milling include power and energy consumption, which vary based on machine type, size, and usage. Efficient use of energy-saving practices and equipment can help reduce overall operational expenses.
Regular maintenance is essential to keep CNC milling machines operating smoothly. Costs include routine servicing, replacement of worn parts, and unexpected repairs.
Quality Control and Inspection Costs
Strict inspection procedures are used in CNC milling quality assurance to guarantee that items fulfill standards. Expenses include labor for inspection, measurement equipment, and setting up quality control procedures to ensure dependability and consistency.
In CNC milling projects, defect prevention and scrap reduction are essential for cost control. This entails spending money on operator training, making use of sophisticated inspection equipment, and putting process enhancements into place to increase accuracy and reduce material waste.
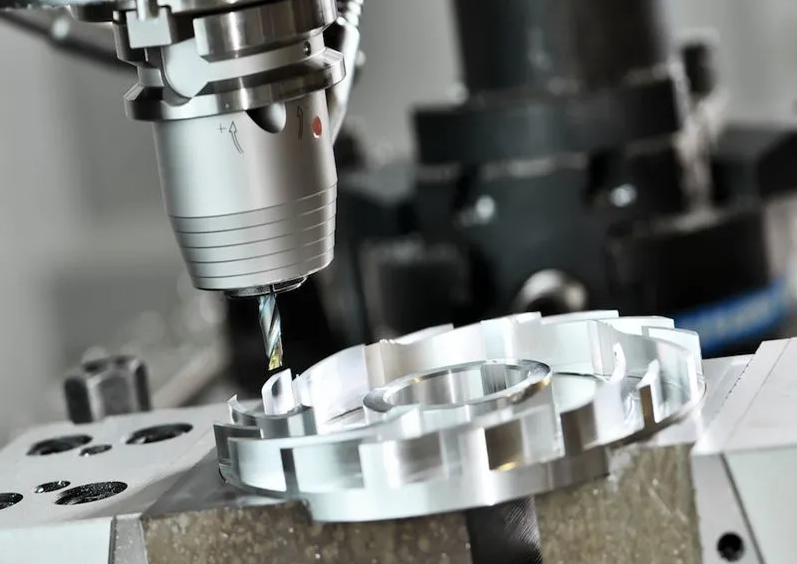
Post-Processing Costs
To achieve desired functionality and aesthetics, post-processing in CNC milling entails finishing operations including polishing, deburring, and surface treatment. Expenses consist of personnel, finishing equipment, and materials utilized in these procedures.
The assembly, packaging, and cleaning of completed parts are all included in the post-machining processes. Expenses include labor, consumables, and overhead associated with processing and getting parts ready for shipping or ultimate usage.
Conclusion and Best Practices
Managing CNC milling costs involves material selection, tooling expenses, setup and programming costs, operational expenses, quality control, and post-processing costs. Efficient CNC milling requires optimizing processes, skilled labor, and advanced technology for competitive advantage and customer satisfaction in manufacturing operations.
About Author:
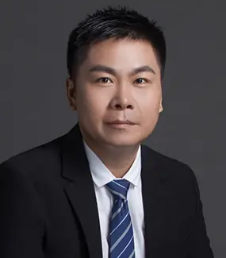
Frank Lee, at the helm of XMAKE, steers the company’s vision with expertise honed over 16 years in the field. A graduate of HIT, he has served as a Lean Manufacturing System expert at General Motors and a global evaluator. Frank has a proven track record of pioneering improvements across 1,000 factories. His extensive experience and leadership have driven significant advancements in manufacturing processes.